Op de valreep van 2018 heeft directeur Fedor Piek een zestal Green Belt diploma’s uitgereikt aan MCB Direct-medewerkers. Met het diploma op zak zijn ze gestart om op de vestigingen verbeteringen te realiseren en verspillingen terug te dringen. Het is de bedoeling dat ze hun ervaringen met elkaar delen. Wij vroegen enkele ‘Green Belters’ naar hun bevindingen.
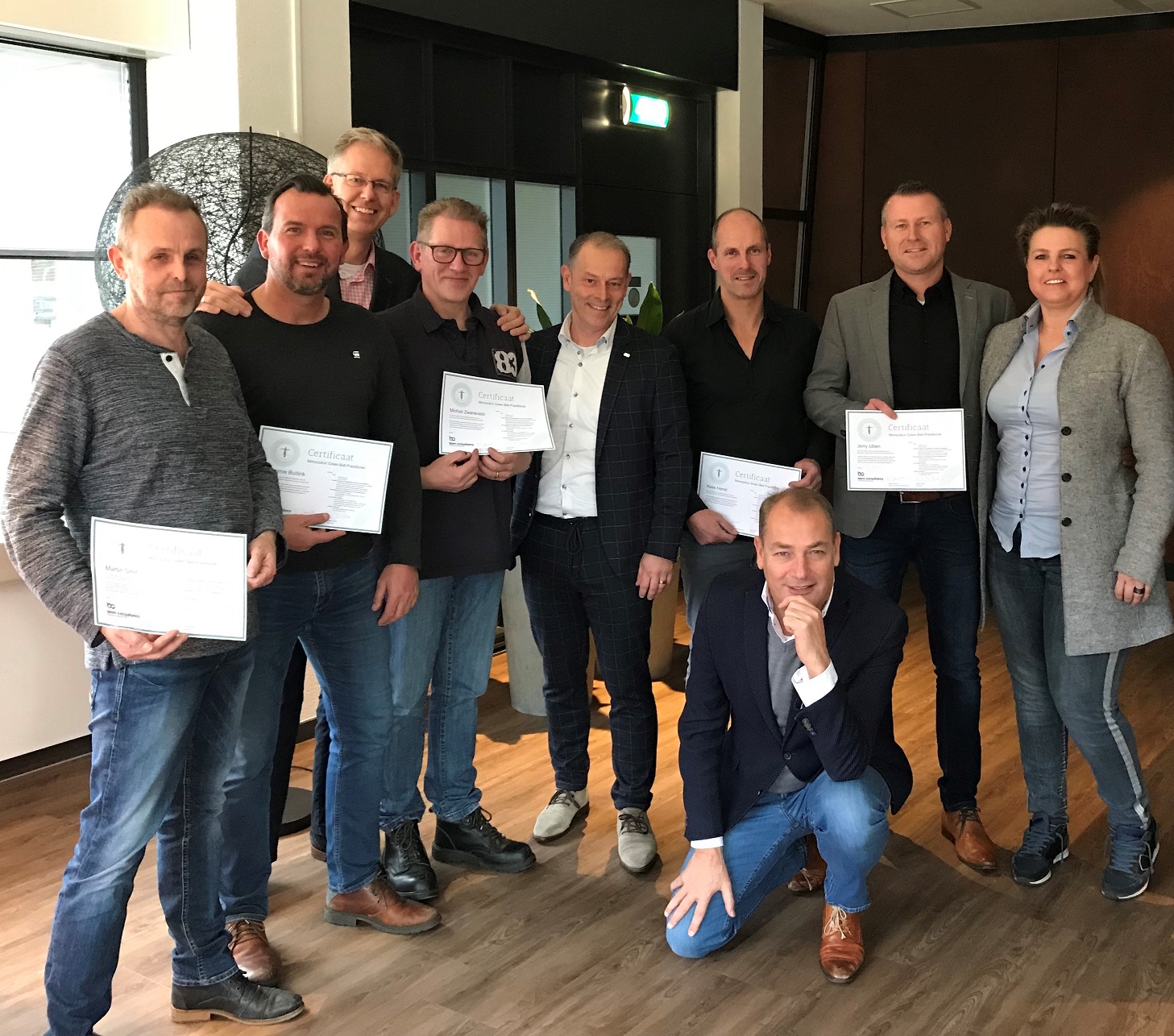
“Wij waren al enige tijd bezig en mede dankzij de ondersteuning van Hilde Vanherck vanuit Forward zijn er op onze locatie al veel fouten uit de productie gehaald. Hierdoor hadden we 5S als onderdeel van de Lean-filosofie reeds aardig in de vingers,” zegt Kees Henst, teammanager Logistiek van vestiging De Kempen. “Door de opleiding zijn we in feite nóg wijzer geworden dan we al waren. De kern van het verhaal is dat we overbodige handelingen uit de processen halen om lagere kosten, hogere productiviteit en kwaliteit met elkaar te verenigen. Je kunt altijd verbeteren. Het zijn vaak kleine stapjes in een continu proces.”
Bordgesprek
Kees houdt elke week een bordgesprek. “Collega’s kunnen dan aangeven of er iets veranderd moet worden waardoor we efficiënter kunnen werken. Je hoopt natuurlijk op het Ei van Columbus. Je moet met elkaar afspraken maken en vastleggen in werkprocedures. Er wordt bij ons echt serieus over zaken nagedacht. Zo was men van mening dat onze kranen sneller moesten kunnen takelen. Daarmee zouden we dagelijks seconden kunnen winnen per hijsbeweging en dat is uiteindelijk maar liefst 1 uur per dag, zo blijkt nu. Die tijdwinst bleek dus te kloppen en er is inmiddels een investering gedaan om de kranen sneller te laten takelen. Op jaarbasis is die winst enorm, dus de investering verdienen we ruimschoots terug en het werk verloopt nu veel vlotter en efficiënter,” verduidelijkt Kees. “Een ander voorbeeld is de aanschaf van een tweede colli-apparaat. We hadden er eentje centraal staan voor de hele hal. Het was vaak zoeken. Nu er een tweede is aangeschaft, hebben we per zaageiland 1 colli-apparaat. Het bespaart tijd en je hebt bovendien geen ergernis van het zoeken.”
Verrijking
Sjimmie Buitink, teammanager Logistiek van de vestiging Achterhoek, had bij een vorige werkgever al kennisgemaakt met Lean 5S. “Ik ervaar deze opleiding als ánders durven denken, met een open mind tegen je werk aankijken. Daarnaast moet je de ruimte krijgen om over zaken na te denken, hoe ze beter en efficiënter kunnen. Het gaat soms om kleine dingen. Als je tien keer op een dag naar een printer moet lopen, kun je je afvragen of de printer niet verplaatst moet worden. Zo maak je werkprocessen slimmer. Zeker als je al jarenlang hetzelfde doet, kan het geen kwaad om eens geprikkeld te worden.”
Sjimmie prikkelt zijn collega’s bewust. “Ik wil mensen mee laten denken als we een probleem hebben gedefinieerd. Samen dieper graven en naar een oplossing zoeken. Zo werd geconstateerd dat de paden voor het picken eigenlijk niet breed genoeg waren. Zowel de handpicker als de picker met de kraan konden niet goed uit de voeten. Met behulp van ‘lean’ kwamen we op het idee om de machines iets te verplaatsen en de stellingen anders neer te zetten. Resultaat is dat we nu bredere paden hebben waardoor we niet alleen sneller, maar óók veiliger kunnen werken. ‘Green Belt’ is echt een verrijking, het maakt je werk interessanter en spannender.”
‘Een mooi staaltje samenwerken’
Martin Smit, teammanager Logistiek vestiging Twente vond de opleiding super leerzaam. “Ik heb vooral geleerd dat we nóg beter moeten communiceren en dat we medewerkers niet alles moeten voorkauwen maar hen zelf moeten laten nadenken over verbeteringen en oplossingen. We doen het best goed maar door ‘lean 5S’ beseffen we dat het altijd beter of in elk geval ánders kan. Dat is geen verwijt, maar realiteit.”
Martin heeft een voorbeeld paraat. “Tijdens een rustig moment in de productie kwam een college naar mij toe. ‘Martin, ik heb eens nagedacht, maar de tafel voor de Shuttle kan beter en veiliger’. Op deze tafel liggen de producten die gereed zijn voor transport met de Shuttle naar andere vestigingen van MCB Direct. Ik stelde voor om het idee in een tekening uit te werken. Het resultaat is dat we nu een vrijwel nieuwe en veiligere tafel hebben met onderstel, die ook nog op wieltjes staat. Hij kan dus verplaatst worden zodat er makkelijk kan worden schoongemaakt. De wieltjes hadden we nog in de kast liggen en één van onze collega’s kon lassen. Een mooier staaltje samenwerking is er niet!”
Wilt u met ons praten over lean en de metaaltotaal-service? Stuur een mail naar nederland@mcbdirect.eu en de juiste vestiging neemt contact met u op.